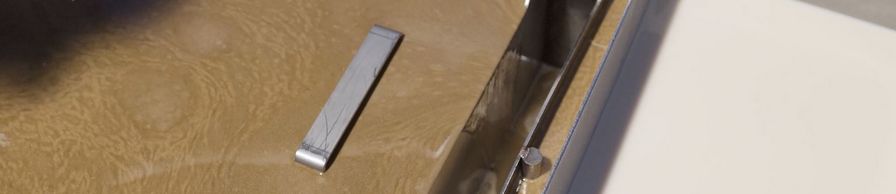
CRS central regeneration systems
Central regeneration system CRS-50 is used for recovery, through a process of separation, filtration and removal of unwanted microorganisms from supplied coolant coming from CNC machining, grinders, milling machines and, if necessary, to prepare completely new coolant of the desired concentration.
The emulsion regeneration system uses technology to remove bacteria and fungi from emulsifying agents used in industry. Microbial removal is done by ozonation of the emulsifying agent in combination with aeration, oxygenation and UV irradiation. The device also removes particulate matter down to the 5-micron level and foreign oils that contribute to the growth of bacteria and fungi.
- Particulate matter filtration,
- Oil separation,
- Removal of microbial formation in the used coolant by ozonation and UV irradiation – optional equipment,
- Improving the concentration of coolant concentrate and water, as well as the new cooling emulsion being prepared, with the “metering station” – optional equipment.
CRS COMPLEX series is used for recovery of overworked medium from processing machines, basic regeneration of used coolants containing a large amount of solid particles and foreign oils, causing a reduction in quality and production standards. Thanks to using appropriate solutions, this device filters and regenerates the recovered emulsion.
- Regeneration from 4 to 20 m³ per day
- Filtration accuracy up to 2 microns (optional)
- Process visualization on the HMI panel
- Remote monitoring of operation and coolant parameters
- Comprehensive reports on water consumption, concentrate, electricity and other parameters
- Central installation of automatic replenishment of coolant in machine tanks (up to 100 machines)
- Automatic operation, IO-link, 4.0 technology
Why is it worth it?
PARTICULATE MATTER FILTRATION
OIL SEPARATION
REMOVAL OF MICROORGANISMS
IMPROVING THE QUALITY OF THE CONCENTRATE
PREPARATION OF NEW COOLING EMULSION
Technical details
ELECTRICAL SYSTEM | |
---|---|
Power supply | 230 VAC, 50 Hz |
Power consumption | 1 kW |
Control voltage | 24 VDC |
Power cord | 3 x 2,5 mm² |
Main protection | B16 |
PNEUMATIC SYSTEM | |
System pressure (supply of pumps and pneumatically operated valve actuators) |
4 - 4,5 bar |
Pressure of the ozone system | 0,3 - 0,5 bar |
TECHNOLOGICAL SYSTEM | |
Max. usable capacity in the “chamber 1” | 1,2 m³ |
Max. usable capacity in the “chamber 2” | 1,2 m³ |
Max. usable capacity in the “oil separator” | 0,05 m³ |
Max. usable capacity of the separated oil tank | 15 l |
System capacity (depending on the condition of the coolant) | 5 m³ / 24 h |
Filtration accuracy |
Depends on the cartridge used by the user F3 filter |
Max. working pressure | 4,5 bar |
Water flow | 20 l/min |
Operating temperature (medium) | 10 - 50°C |
Performance of ozone generator - optional equipment | 6 - 7 g/h |
Separation of foreign oils | 90 % |
Removal of microorganisms - optional equipment | 95 % |
Suction height from the “tank 1” (IBC 1000) | 5 m |
Discharge height to the “tank 2” (IBC 1000) | 5 m |
Material | Stainless steel |
ELECTRICAL CONNECTION PARAMETERS | |
---|---|
Supply voltage | 230 VAC, 50 Hz, 20 A |
Power cord | 3 x 2,5 mm² |
Main protection | B20 |
Max. ambient temperature range | +5°C to +40°C |
PARAMETERS OF PNEUMATIC CONNECTION | |
Connection diameter | Ø 12 – ½” |
Required pressure | 6 - 10 bar (0,6 - 1 MPa) |
Required flow rate | 1000 NI/min (1 m³ / min) |
DIMENSIONS AND WEIGHT | |
---|---|
Weight (with empty tanks) | 450kg |
Dimensions (L x W x H mm) | 1532 x 1560 x 1500 |